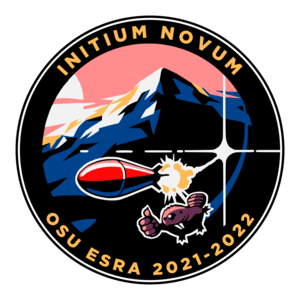
College of Engineering Unit:
The OSU ESRA team has been a pioneer in student rocketry since the conception of the OSU AIAA chapter. ESRA (Experimental Sounding Rocket Association) annually assembles the greatest collegiate rocket building teams in national competition, and OSU has competed with outstanding success since 2013. This year’s competition will be held at Spaceport America in late June, where OSU will be attempting to launch to 30,000 ft. with a 8.8 lb payload and student-built motor.
What We Build
There are two primary concerns in rocketry: getting the rocket up, and getting it back down. Years of rocketry experience and simulation data were brought together to create the aerodynamic design. Weight, stability, pressure, temperature, and more factor into the success of a rocket, and all systems must work in unity to perform as desired. A cutaway view of the rocket is attached at the bottom of this page.
The Motor
The lower body tube of the rocket houses the motor assembly, which is ignited to put the rocket into the sky. The OSU ESRA team researches and manufactures a solid rocket motor. The propellant consists of a hydroxyl-terminated polybutadiene binder, aluminum fuel, ammonium perchlorate oxidizer, and an isocyanate curative. This propellant is packed and hardened into six cylindrical grains which are then placed into a fiberglass thermal liner that sits within an aluminum motor casing. An aluminum forward enclosure is placed ahead of the grains to help maintain motor pressure and allow for data collection. A graphite deLaval (converging-diverging) nozzle is placed at the aft end of the motor casing to direct the flow of burning propellant and provide thrust. Test fire data indicates that this motor is capable of delivering over 33,000 Ns of impulse and 1800 lbf of thrust.
The Recovery
The remainder of the rocket is concerned with safe recovery. Rockets flying to this altitude must utilize dual deployment, where a small drogue parachute deploys at apogee and a larger main parachute deploys around 1500 ft, so that the rocket is not blown miles away by the wind. The upper body tube rests between these sections, where the flight computer in the avionics bay transmits the rocket’s location, altitude, velocity, and more. The computer also triggers small explosives that separate the body tubes at apogee and the nose cone main parachute deployment.
The Payload
Along with the main parachute, a payload is deployed, which separates entirely from the rocket and descends on its own parachute. This payload is engineered with the ability to plant, water, and fertilize a load of seeds, simulating the prospective reality of interplanetary agriculture.
Project Website(s):
Project Communication Piece(s):
Attachment | Size |
---|---|
![]() | 3.76 MB |
![]() | 208.51 KB |