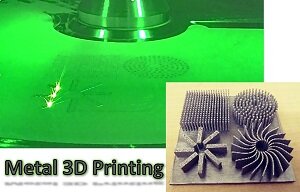
Oxide dispersion strengthened (ODS) FeCrAl alloys are promising candidates for harsh environments due to their high strength and oxidation resistance at elevated temperatures. Conventionally, mechanical alloying of FeCrAl with yttria nanoparticle followed by hot consolidation was used to manufacture ODS FeCrAl alloy. However, Conventional methods for manufacturing of ODS alloys involve too many costly and time-consuming steps, contamination during mechanical alloying, and heterogeneous distribution of nanoparticles. 3D printing/Additive manufacturing can be a potential method for eliminating of all drawbacks of conventional manufacturing of ODS FeCrAl by using commercially available FeCrAlY powder in 3D printer. This work aimed to adopt additive manufacturing, in particular, selective laser melting (SLM) to investigate the feasibility of manufacturing ODS FeCrAl alloys via internal oxidation. Such that, FeCrAlY powder was used in presence of residual oxygen inside the SLM chamber with no additional need for mechanical alloying with yttria nanoparticles. Gas-atomized Fe–24Cr–8Al–0.5Y (wt.%) powder was procured from Oerlikon Metco (D50=33 microns) and characterized for morphology, powder size, and size distribution. Cylindrical samples were built via SLM using Coherent/OR Creator. The highest density of 98.0%±0.4 was obtained for the sample printed at scan speed 100 mm/s with hardness of 335±8 HV. Spherical nanoparticles of size 20-100 nm implied that Al and Y precipitated in-situ within the matrix during solidification of SLM process. Therefore, ODS FeCrAlY was successfully in-situ manufactured via SLM.