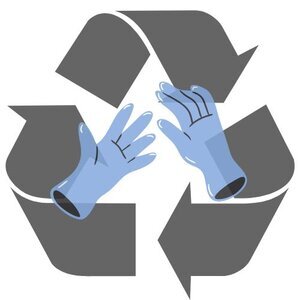
Technical Description
Single-use disposable gloves are a major contributor to landfills and a major source of plastic pollution. The proposed reusable medical and lab gloves can solve this problem and revolutionize the industry by reducing waste like never before. This product will be made from thermoplastic vulcanizate (TPV), a durable and heat-resistant thermoplastic elastomer. These gloves will come in five sizes coordinated by color and will be around 10 mils (0.254 mm) thick.
After use, they will be sterilized by autoclave because this device is already used by the target clientele to sterilize hazardous materials. Models used to test the glove’s feasibility include glove elongation, permeability, and heat resistance. Other models that will be considered are biocompatibility, biohazard resistance, and tensile strength testing before and after autoclaving. Based on these models human factors are considered to be low risk for harm or abuse to individuals.
Design improvements that still need to be assessed are as follows: unfolding of used gloves, reorganization into packaging, and recycling the material for use in future glove production. We have identified several possible solutions for unfolding the used gloves and reorganization into packaging include using pressurized air and packing into a tissue-like box, respectively. Environmental impacts center around the energy costs used to make, produce, and re-use the gloves. These costs will also be in consideration for improvement as this design continues to change and adapt to better counteract the problem disposable that gloves present.
Results obtained from testing were categorized under these models. The creation of gloves was done with a heated press to make 24 circular films of the TPV. The material was then autoclaved 10 times to simulate repeated use of the material and test the mechanical properties. Qualitative studies found that the material did not change in elasticity or strength when in comparison to the non-autoclaved films. Chemical permeation tests on 3 chemicals were done and were FDA compliant except for the 10x autoclave for hydrochloric acid. Elongation was tested and found to be on average 100% which is much less than the FDA requirement of 400%. More testing needs to be done on a larger sample pool with more uniform films to fully test the capabilities of the material.
We estimate that this material will be able to withstand and pass the testing requirements characterized by the FDA when mixed with a small amount of nitrile or latex, and with consistent use and sterilization.
General Description
Single-use disposable gloves are a major contributor to landfills and a major source of plastic pollution. The proposed reusable medical and lab gloves can solve this problem and revolutionize the industry by reducing waste like never before. This product will be made from thermoplastic vulcanizate (TPV), a durable and heat-resistant thermoplastic elastomer. We estimate that this material will be able to withstand and pass the testing requirements characterized by the FDA when mixed with a small amount of nitrile or latex, and with consistent use and sterilization. These gloves will come in five sizes coordinated by color and will be around 10 mils thick, or 0.254mm.
After use, they will be sterilized by an autoclave, a device that sterilizes equipment using heated pressurized steam. This device is already used by the target clientele to sterilize hazardous materials. Models used to test the glove’s feasibility include glove elongation, permeability, and heat resistance. Other models that will be considered are biocompatibility, biohazard resistance, and tensile strength testing before and after autoclaving. Based on these models human factors are considered to be low risk for harm or abuse to individuals.
Results obtained from testing were categorized under these models. The creation of gloves was done with a heated press to make 24 circular films of the TPV. The material was then autoclaved 10 times to simulate repeated use of the material and test the mechanical properties. Qualitative studies found that the material did not change in elasticity or strength when in comparison to the non-autoclaved films. Chemical permeation tests on 3 chemicals were done and were FDA compliant except for the 10x autoclave for hydrochloric acid. Elongation was tested and found to be on average 100% which is much less than the FDA requirement of 400%. More testing needs to be done on a larger sample pool with more uniform films to fully test the capabilities of the material.
We estimate that this material will be able to withstand and pass the testing requirements characterized by the FDA when mixed with a small amount of nitrile or latex, and with consistent use and sterilization.
K-12 Description
Single-use disposable gloves greatly contribute to landfill pollution on our Earth. These types of plastic gloves are often used in nurses offices, when you go visit a doctor, as well as the gloves worn by dentists. These professionals use plastic gloves that take many years to decompose into the Earth, and might not fully decompose at all. We have proposed a solution for this plastic waste problem: a reusable glove made from thermoplastic vulcanizate also called TPV. This type of plastic is resistant to heat, elastic, and can easily degrade into the Earth after a short period of time. A new type of glove made from TPV that can be reused could cut down on the plastic pollution that comes from plastic gloves.
After the gloves are used, they will be sterilized by autoclave, a device used to clean lab and hospital materials to make sure that they do not spread any infections after being disposed of. To ensure that these gloves would be safe for repeated use, we developed three testing models to test the glove’s stretchiness (elongation), permeability (how easily liquids can pass through the glove), and heat resistance. We also considered testing for allergic reactions, blood and bodily fluid resistance, and the strength of the gloves both before and after autoclaving. These gloves will come in five sizes coordinated by color and will be around 0.254 mm thick.
We created 24 circular films of TPV by placing plastic beads on a heated plate and pressing the two plates together. The plastic beads were melted together to create a circle that we then cut in half to give us 48 total testing samples. Some of the samples were autoclaved 10 times in order to test the repeated use of the material through wear and tear. Our studies found that after these 10 runs, the material did not change in its stretchiness (elongation). For the permeation test (when a liquid is passed through the material), we tested 3 different chemicals and found that all but one of the samples passed according to the FDA. The only sample that did not pass was one that was run in the autoclave 10 times and exposed to the chemical hydrochloric acid. The elongation tests and found that the average glove only stretched 100% (doubled in length) which is much less than the FDA requirement of 400% (4 times the original length). Based on these results we concluded that more testing needs to be done with more samples to find out if the material will work.
We estimate that this material will be able to withstand and pass the testing requirements described by the Food and Drug Administration when mixed with a small amount of other elastic materials, and with consistent use and cleaning.
Attachment | Size |
---|---|
![]() | 1.68 MB |