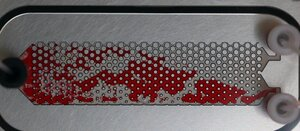
Separations processes account for 10-15% of the world’s energy consumption. Notoriously, traditional liquid-liquid extraction (LLE) processes get costly with process intensification at higher surface area. A newly developed process that utilizes Multiphase-Microchannel Separators (MMS) fits in the liquid-liquid extraction processes small-scale category to provide lower cost alternatives. This process is different than a conventional LLE in that it does not rely on separation by a difference in density or boiling point, but by a difference in wettability, where across a plate, there is a gradient of capillary force.
One advantage of the MMS over traditional extraction techniques is modular design, allowing for increasing and decreasing the flow capacity with ease, while standard techniques are fixed in capacity once a vessel is manufactured. MMS can reduce retention times to less than 3 seconds where traditional LLE could be up to 15 minutes. MMS systems also require zero energy input. Additionally, different parameters are important for efficiency of the MMS, so separations that are not possible with traditional methods may function well in an MMS.
For this project, a client requires isopropyl alcohol (IPA) to be recovered from an aqueous feed stream. The two different processes, a traditional LLE and an MMS, are modeled in Aspen Plus and then compared on performance and economics. In Aspen Plus, a “decanter” is used for the separation unit to model the complete equilibrium seen in the MMS. For the LLE process, the feed stream goes through the LLE and then to a distillation column which produces 80 wt% product and recycles solvent back to the fresh solvent feed. The MMS works similarly but differs by having two decanters in series where the extract of the first decanter mixes with the extract of the second decanter to increase separation. This is fed to a distillation column where the IPA is separated from the solvent to 80 wt% IPA, whereas the solvent is recycled back to the beginning of the process.
Preliminary design results show that the performance of the MMS is similar to the LLE except that more solvent is required thus creating a raw material cost. Future work will be in manipulating the solvent to aqueous feed flow ratio to reduce this solvent requirement while still achieving high performance specs. Also, an economic analysis will be completed comparing the CapEx and OpEx of the MMS LLE process to the conventional LLE process for the project statement above. Research and a recommendation will be reported for this MMS project that show its capabilities and possible opportunities as a liquid-liquid separation process.
Attachment | Size |
---|---|
![]() | 551.27 KB |