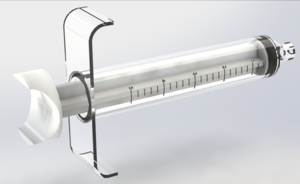
Current syringes present many problems, to the environment and to the consumer. Single use plastic is a major contributor to ocean pollution and non-biodegradable single use syringes add a large volume of plastic to the environment that won’t degrade for centuries. Additionally, the small handles on current syringes are not designed with the human hand in mind, and can make it difficult for people with limited mobility to use. While latex is biodegradable, syringes with latex based gaskets can even cause an adverse reaction to people with latex allergies. Upon seeing these problems with current syringes in the market we decided to address these problems holistically, making a product that is biodegradable, ergonomic, and conscious of latex allergies. This term, we successfully created a functional biodegradable syringe from concept to physical prototype over the span of 20 weeks. The first prototype in SolidWorks using the stress testing indicated that our product would be able to withstand the plunging force as long as the thickness of the syringe barrel is thick enough. However, for large scale manufacturing the syringe will be injection molded instead of 3D printed. Next, the second prototype which was the ergonomic grip focus testing resulted in a final design for both the barrel grip and the plunger grip. The grip designs were the half-pipe for the plunger and the flared barrel grip. Finally, for the third prototype the degradation testing did not yield the results that matched literature as the PLA did not degrade very much or at all in the soil and seawater. The reason for this is that potentially the seawater and the soil did not contain the microbes that breakdown PLA. In the future, we would want to test our prototypes again, but using injection molding instead of 3D printed PLA. Injection molding PLA has different structural and material properties than 3D printed PLA therefore testing the prototypes again allows us to create a product that meets the opportunity and customer needs.
Attachment | Size |
---|---|
![]() | 464.66 KB |
![]() | 56.23 KB |
![]() | 57.43 KB |