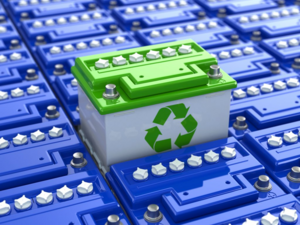
Lithium-ion battery (LIB) recycling has become an area of interest with the fast-paced growth of the electric vehicle industry. Tesla alone is anticipating to produce 20 million EVs annually by 2030 [1]. Other companies are expected to follow suit. With the rise in battery powered devices and vehicles, concerns have been raised for environmental impact of the EV batteries, which are typically made of cobalt, nickel, and manganese. Cobalt, in particular, is a high-value battery component sourced from the Democratic Republic of Congo, where political instability causes price fluctuations and loose labor laws create ethical issues around cobalt supply [2]. The environmental impact and economic cost of sourcing elements such as lithium and cobalt can be reduced by recovering these materials from spent batteries, which will also help to reduce landfill waste.
Current recycling methods for electric vehicle LIBs include: pyrometallurgy, hydrometallurgy, and direct recycling. Hydrometallurgical processes involve leaching, extraction, and precipitation for recovering valuable metals. Compared to other metallurgical methods of separation, it is preferred for its high recovery efficiency as well as reductions in energy consumption and emissions. The hydrometallurgical operation also offers more possibilities for anode material recovery as well, improving potential for profitability in the graphite anode. A drawback to the leaching process is the use of solvents, which increases costs due to the need for additional processing prior to disposal.
Recycling plants for electric vehicle Li-ion batteries exist, but improvements in efficiency and profitability are needed before large scale recycling programs are implemented. Our project aims to explore how hydrometallurgical methods may be employed to recycle used lithium-ion batteries. Battery recycling offers opportunities in reclamation of valuable materials, like lithium and cobalt, that can be applied to different industries in need or in producing more batteries to aid in the upcoming demand.
In the development of our plant design, we aimed to develop a scaled-up process of laboratory scale hydrometallurgical processes for the recycling of electric vehicle LIBs. Spent LIBs undergo mechanical pre-treatment where they are crushed and ground into a powder, then sieved to recover the cobalt-rich fraction with a particle diameter of less than 1 mm. Hydrochloric acid is then used to leach cobalt from the electrodic powder in a mixer-settler unit, resulting in an aqueous leach solution. This enters a second mixer settler unit where cobalt is stripped from the aqueous leach solution using an mixture of 20 vol% Di-(2-ethylhexyl)phosphoric acid (D2EHPA) diluted in kerosene in an organic to aqueous feed ratio of 1:1. Through the subsequent drying process, a solid cobalt product is obtained. In order to be profitable, a plant should process at least 2,500 tons of batteries per year. Our project focuses on the design of the two mixer-settler units used for leaching and extraction for a plant which has a capacity to process 10,000 metric tons of spent batteries per year.
[1] Z. Shahan, “Elon Musk: Tesla Aiming For 20 Million Vehicles/Year By 2030,” CleanTechnica, 03-Oct-2020. [Online]. Available: https://cleantechnica.com/2020/10/02/elon-musk-tesla-aiming-for-20-million-vehicles-year-by-2030/.
[2] A. Home, “Cobalt, the heart of darkness in the shiny electric vehicle story: Andy Home,” Reuters, 28-Nov-2017. [Online]. Available: https://www.reuters.com/article/us-cobalt-supply-ahome/cobalt-the-heart-of-darkness-in-the-shiny-electric-vehicle-story-andy-home-idUSKBN1DS316.
Attachment | Size |
---|---|
![]() | 23.51 MB |